Precision Plastic Injection Molding: A Game Changer for Metal Fabricators
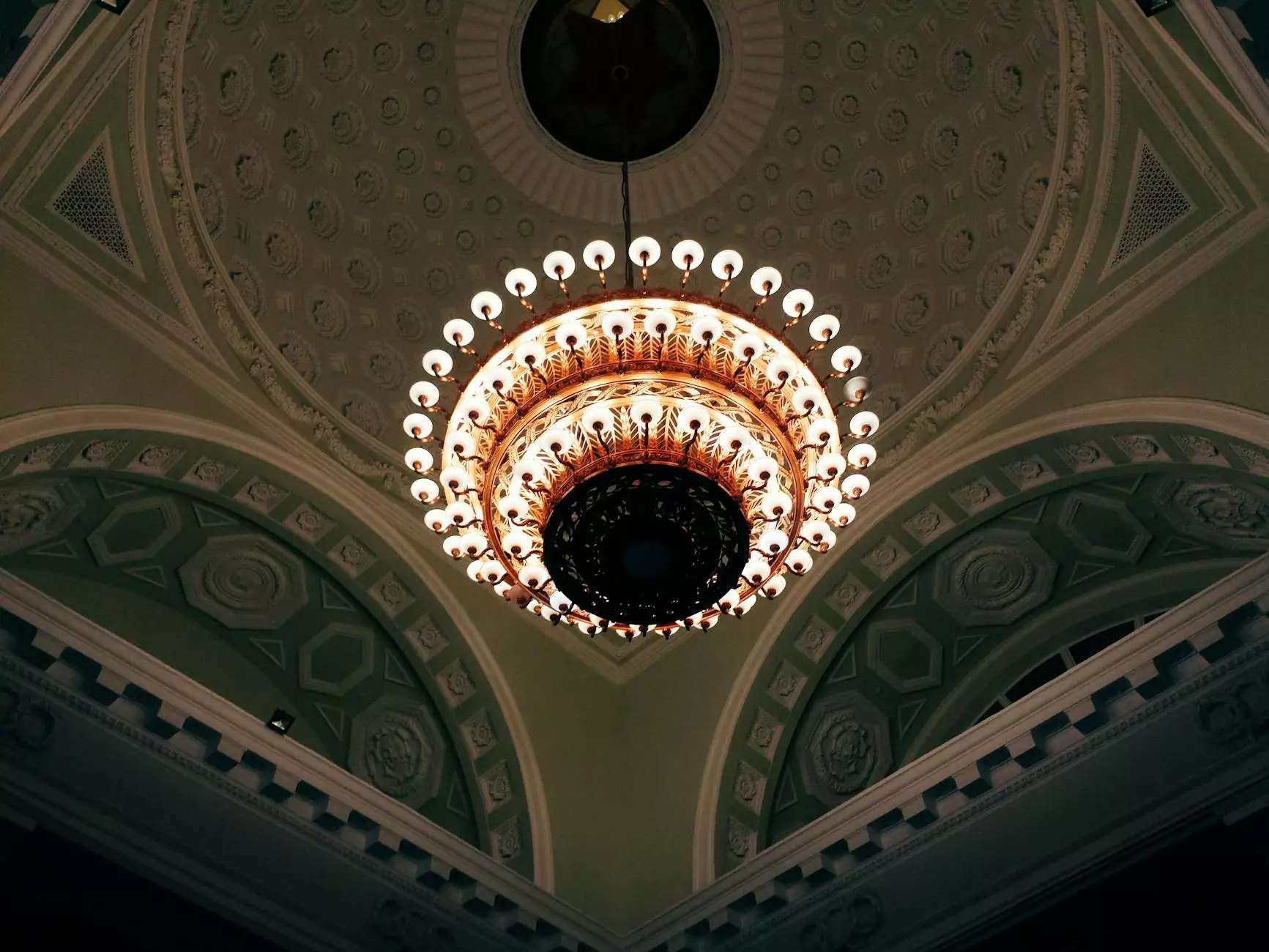
Understanding Precision Plastic Injection Molding
The world of manufacturing has evolved significantly, and precision plastic injection molding stands out as an innovative process that has revolutionized production capabilities. This technique is not just about creating plastic parts; it’s about achieving high precision, consistency, and efficiency in manufacturing.
At its core, precision plastic injection molding involves the manufacturing of components by injecting molten plastic into a mold. Once the plastic cools and solidifies, it takes the exact shape of the mold, allowing for intricate designs and precise dimensions. This process is essential for producing detailed parts that meet stringent industry standards.
The Process of Precision Plastic Injection Molding
The steps involved in precision plastic injection molding can be broken down into several key phases:
- Mold Design: Creating a mold is the first and most critical step. The design must reflect the exact specifications needed for the end product.
- Material Selection: Various types of plastics can be used based on the required properties of the final product, such as flexibility, strength, and durability.
- Injection Phase: The selected plastic is heated to its melting point and injected into the mold at high pressure.
- Cooling Phase: The injected plastic cools and solidifies, taking on the shape of the mold.
- Demolding: Once cooled, the mold is opened, and the newly formed part is ejected.
- Quality Control: Each component undergoes inspection to ensure it meets the necessary quality standards.
This meticulous process ensures that precision plastic injection moldings are produced with utmost accuracy and can meet the varied demands of the market.
Advantages of Precision Plastic Injection Molding
Utilizing the precision plastic injection molding technique offers numerous advantages, especially for metal fabricators looking to diversify their production capabilities:
- Cost-Effective Production: Once the mold is designed and created, the cost of producing additional parts is significantly lower compared to other manufacturing processes.
- High Precision: This process allows for intricate designs with tolerances as low as ±0.001 inches, making it ideal for precision components.
- Complex Shapes: The molding process enables manufacturers to produce complex and intricate shapes that rigid alternatives cannot offer.
- Material Versatility: A wide range of thermoplastics and thermosetting plastics can be utilized, giving designers the flexibility to choose materials best suited for their applications.
- Efficiency: The cycle time for molding can be very short, resulting in faster overall production times.
- Minimal Waste: The process generates less waste compared to traditional machining methods, making it more sustainable.
These advantages make precision plastic injection molding a preferred choice across various industries, including automotive, consumer goods, and electronics.
Applications of Precision Plastic Injection Molding
The versatility of precision plastic injection molding allows it to be employed in a plethora of applications:
Automotive Industry
In the automotive sector, it is utilized for components such as dashboards, bumpers, and various interior parts. These parts require strict adherence to specifications, and injection molded plastics offer both strength and aesthetic appeal.
Medical Devices
With stringent regulations governing medical device manufacturing, precision injection molding enables the production of highly regulated components such as drug delivery systems and surgical tools with exceptional quality assurance.
Consumer Electronics
From mobile phone casings to internal components, precision plastic injection molding is prevalent in the production of electronic devices, ensuring high aesthetic quality and functionality.
Packaging
Packaging solutions such as containers and lids often utilize injection molded plastics for their durability and versatility, catering to various industries such as food and pharmaceuticals.
Household Products
Everyday items like toys, kitchenware, and storage solutions are often produced via this method due to its efficiency and ability to produce lightweight yet durable products.
Challenges in Precision Plastic Injection Molding
Despite its advantages, precision plastic injection molding does come with its challenges:
- Initial Investment: The cost of designing and producing molds can be high, which may deter some companies from utilizing this technology.
- Design Limitations: While the method allows for complex shapes, there are still design limitations that engineers must take into account, such as mold release angles and wall thickness.
- Material Selection Issues: Choosing the right material is crucial, as not every plastic is suitable for every application, and can lead to performance issues if mismatched.
- Quality Control: Maintaining quality standards requires rigorous testing and monitoring throughout the production process, which can be resource-intensive.
Addressing these challenges requires expertise and a commitment to quality, attributes that metal fabricators can well leverage alongside their existing capabilities.
The Future of Precision Plastic Injection Molding
The future of precision plastic injection molding looks promising, with advancements in technology such as:
- Automation: The integration of robotics and automation technology is streamlining the molding process, improving efficiency, and reducing manpower costs.
- 3D Printing: Utilization of 3D printing technology is becoming common in mold design, allowing for rapid prototyping and reduced lead times.
- Bioplastics: A growing trend towards sustainability means there is increased interest in using biodegradable plastics and recycled materials in the molding process.
- Smart Manufacturing: Advances in IoT and data analytics are being used to monitor processes in real-time, improving output quality and operational efficiency.
These innovations are not just enhancing productivity but also molding the industry into a more sustainable and efficient sector.
Conclusion: Embracing Precision Plastic Injection Molding
For metal fabricators looking to expand their product offerings or improve production efficiency, precision plastic injection molding represents an opportunity that cannot be ignored. It allows for the production of high-quality, precise, and complex components that meet the diverse needs of today’s industries.
As technology continues to evolve, embracing innovations in injection molding will enable businesses to stay competitive in a rapidly changing market. By investing in this advanced manufacturing technique, companies can enhance their operational capabilities while delivering superior products to their customers.